In the July 2020 edition of Modern Metals, a featured article was published with ArcelorMittal Tailored Blanks (AMTB) along with their partner RDI Laser Blanking Systems. The article highlights how we helped AMTB with cost effective, quick turnaround of development parts using coil-fed laser technology. We have been working together for several years and provided tailored blanks to the automotive industry.
RDI entered the toll processing industry by providing contract laser blanking a few years ago. This enabled customers to utilize RDI’s coil-fed laser blanking technology as a service for their part production needs. Customers out of the US, Mexico, and Canada were sending coils to be laser cut by RDI out of our facility near Chicago, Illinois. The demand for this technology was a result of the scrap savings, the elimination of hard tooling costs, and dimensionally accurate parts. By offering contract blanking, it allowed us the opportunity to further improve our equipment offering.
For example, the materials processed range from diamond plated aluminum, stainless steel, AHSS, UHSS and even titanium. Running these various material types helped us further develop the right settings and assist gas for best edge quality and speed. These settings are saved in our database for future use and can be shared with our customers who have our equipment. This service helped our customers produce great parts while also enabling us to fine tune our technology offering.
When AMTB needed to provide welded blanks for their automotive customers, they put their trust into RDI to not only cut the blanks, but to also provide quick turnaround using their highly flexible coil-fed laser technology. ATMB was able to modify their customer’s designs on the fly and save on the costs by forgoing trim die changes.
By toll processing, we learned everything about what our customers go through. It’s a much faster feedback cycle. We can relate to customers’ challenges since we may have come across them, too.
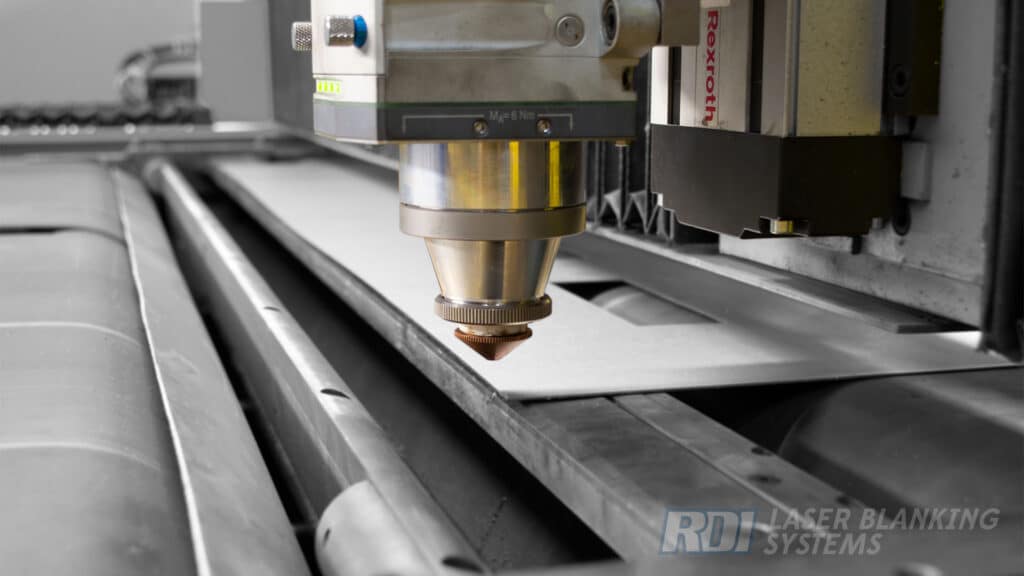