Laser flashback is a defect where parts have weld points between the bottom of the material and the support structure. It can cause molten metal to erupt to the top surface of the part, causing puddle-shaped marring on the finished edge. This is a known problem with certain sheet metal cutting applications that utilize laser cutting slats. There are workarounds and solutions to avoid this.
When cutting material, the material must be supported underneath to be cut. This is true for lasers or for saws or any cutting process. In carpentry, when a board is cut, the carpenter will often use a sawhorse to support the board on both sides. This is important to cut over open air so that the saw does not cut into the supports underneath. With laser cutting, the material needs to be supported as well.
What are the headaches with laser cutting slats?
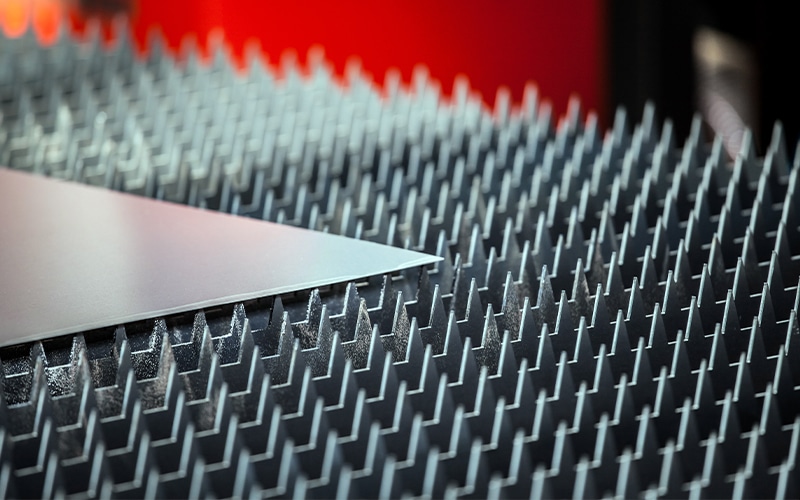
For table laser manufacturers, a series of slats support the material. They are sometimes also referred to as a bed of nails. However, these laser cutting slats present a problem when cutting shapes: Flashback. Flashback occurs when the laser beam passes over a supporting slat while in the process of cutting a part.
A laser cutter takes a focused beam of laser light and uses it to melt or vaporize the material. The laser is emitted from a cutting head where the beam of light is centered in a nozzle. A stream of compressed gas (like Shop Air, Nitrogen, Oxygen, or Argon) flows out of this nozzle. This gas pushes the molten material out of the cut width (also known as the kerf). The gas pressure, nozzle diameter, lens focus & centering, and nozzle standoff are among several parameters that are carefully controlled to ensure good cut quality.
Laser cutting parameters are carefully controlled to cut through the material at its specific thickness. When the laser light runs into the slat, the energy does not fully melt through it. As a result, it can partially melt the support slat. The flow of molten metal from the kerf at this point may act like a clog, and the assist gas will force this molten metal to come up to the top and may cause a small weld between the slat and the workpiece.
Why is Flashback bad?
For some non-surface critical applications, it may be acceptable to have small marks on the back surface of parts.
Even in these non-surface critical applications, flashback can wreak havoc with automated part removal. The laser cutting slats will occasionally weld to the parts. This can reduce reliability of automated part removal.
Slag
The buildup of the material on the slats is called slag or dross. Those operating table lasers need to continually clean the slag off of the slats. Replacement of the slats will need to happen periodically. The slag build up or slat replacement can drive an inconsistent bed. This can cause more problems with a sheet not lying perfectly flat.
Surface critical parts have added concerns in that the flashback can cause parts to fail cosmetic standards due to marks on the bottom surface.
How does RDI Laser Blanking Systems eliminate flashback?
As opposed to a system like a table laser with laser cutting slats, RDI Laser Blanking Systems use an innovative approach. The system will eliminate flashback and surface scratching. There are many other benefits to this configuration to further improve sheet metal processing when compared to table lasers.
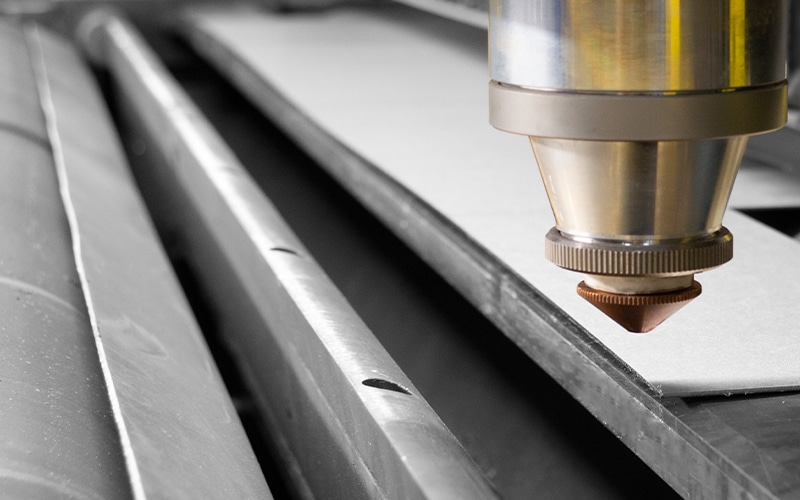