
Coil-Fed Laser Blanking Technology has many benefits that can help you in your manufacturing processes. In this scenario, we evaluate a 32” diameter circular part, commonly found in the cookware industry. Our analysis is with a 60” wide, 0.030” thick stainless steel coil compared to sheets using traditional table lasers.
SHEET ANALYSIS (TABLE LASER) TECH
Length | Part Quantity | Scrap % |
---|---|---|
120″ (Standard) | 6 | 33.139% |
112.5″ | 6 | 28.681% |
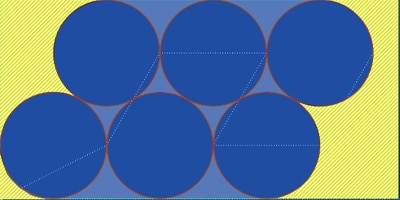
COIL ANALYSIS (COIL-FED LASER)
Length | Part Quantity | Scrap % |
---|---|---|
1,637ft | 1,218 | 16.739% |
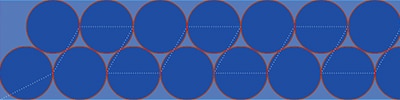
COIL ANALYSIS (COIL-FED LASER)
Sheet Quantity | Weight | Length | Part Quantity | Scrap % |
---|---|---|---|---|
Coil-Fed1 (Continuous Strip) | 10,000lbs | 1,637ft | 1,218 | 16.739% |
Sheet | 10,000lbs | 1,637ft | 978 | 33.139% |
Producing metal blanks using coil-fed laser blanking technology allows for greater material optimization, that will save you money. The savings in this scenario is 1,640lbs less scrap. The result is a 49.5% scrap improvement when utilizing coil-fed laser blanking technology. The ability to cut parts edge-to-edge from slit to width coils can result in even further savings in certain scenarios.
OUTCOME: SCRAP IMPROVES 49.5%
WHEN UTILIZING COIL-FED LASER BLANKING TECHNOLOGY
Scrap savings is one of the many advantages of using coil-fed laser blanking technology over traditional laser blanking methods.
To learn more about our coil-fed laser blanking solutions,
please fill out our Contact Form or give us a call at (630) 274-0600